When it comes to lightweight technology, everyone is no stranger to it. As one of the core technologies of new energy vehicles, it is the only way to achieve energy conservation, emission reduction, green development, and the promotion of a win-win situation for the automotive industry. It has now become a new energy vehicle manufacturing industry. The company's "point of deer".
Lightweight is the trend
In fact, as far as new energy vehicles are concerned, the weight of a single component, the power battery, is as high as hundreds of kilograms. It is conceivable that the weight of the entire vehicle is at least a ton. Research abroad has shown that if the vehicle's vehicle weight is reduced by 10%, the energy efficiency can be increased by 6% to 8%. This shows that it is significant in terms of reducing energy consumption, reducing exhaust emissions, and increasing the mileage of power batteries.
In recent years, China has introduced a number of policies and environmental protection standards to promote the research and development of new energy vehicles, and gradually promote the process of lightweighting automotive materials. In September 2017, the "Measures for the Concurrent Management of the Average Fuel Consumption of New Passenger Vehicles and New Energy Vehicles" published by the Ministry of Industry and Information Technology and the Ministry of Finance and other agencies also injected a boost to the development of new energy vehicles. It is expected that by 2020, the demand for vehicle weight reduction will become increasingly prominent.
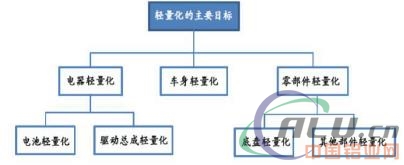
As we all know, the power consumption, exhaust pollution and short driving range are the “pain points†of new energy vehicles. For manufacturers, in order to better meet the market demand, the popularity of lightweight technologies has become imminent.
In order to achieve vehicle weight reduction, people in the industry have summarized three ways:
The first application of high-strength and lightweight materials (methods), such as high-strength steel, ultra-high-strength steel, aluminum alloys, magnesium alloys, engineering plastics and fiber-reinforced composite materials. From the technical perspective, carbon fiber composite materials, aluminum-magnesium alloys, and advanced high-strength steel are currently the three major directions explored by auto companies. These three materials can replace 60%, 40%, and 25 percent of the current mainstream material low carbon steel. %.
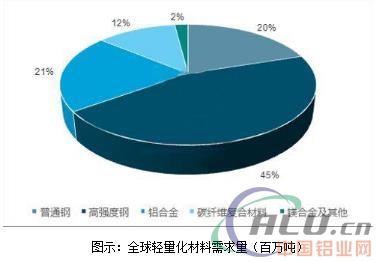
Second, optimize the lightweight design of the body structure (premise), use structural analysis and CAD, CAE and other technologies to optimize the design of the structure, in order to reduce unnecessary materials, reduce wall thickness, reduce the number of parts, etc., such as: modular integration design Structural topology optimization.
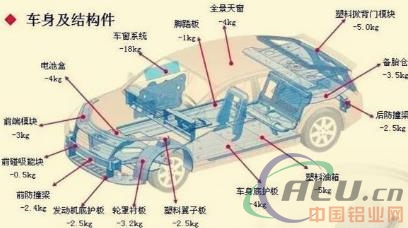
Illustration: The automotive exterior parts are made of plastic steel and plastic lightweight optimization technology to achieve a cumulative weight reduction of 60Kg or more.
Third, the use of advanced manufacturing technology (safeguards), such as laser welding, roll forming (advanced molding technology to ensure the safety of the entire vehicle structure), high-strength steel thermoforming, internal pressure forming and other advanced manufacturing technologies, Structural adhesive bonding and riveting of dissimilar materials and other advanced connection technologies.
Assisting enterprises in "internal and external cultivation"
In the process of concrete implementation of lightweight technology, automobile manufacturers must reduce the weight of their parts, but they must not reduce the strength of their parts, and strive to make new energy vehicles “inside and outsideâ€.
In 2016, Volvo announced that the battery weight of electric vehicles has entered the practical test phase. The relevant responsible person said in an interview with the Electric Vehicle Resources Network that “If the current electric vehicle batteries are all replaced with new lightweight materials, the vehicle weight can be reduced. More than 15%, in addition, the material cost is lower and more environmentally friendly.â€
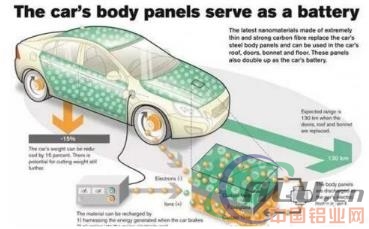
Icon: Lightweight components for Volvo cars
It is true that there is a large gap in the lightweighting of power batteries in China, but manufacturers such as Changan Automobile and Beijing Automotive New Energy have also made efforts in lightweight materials and lightweight structure design.
In mid-December, BAIC New Energy selected a joint venture with the world's lightweight technology team (a team of Huffin Bahrain academicians) to build the Beiqi New Energy Dresden Lightweight Technology Center, which will focus on multi-material lightweight vehicles and carbon fiber composite materials. Cooperative research and development is carried out in the areas of bodywork and chassis components, and it is planned to achieve the first batch of project technical achievements in 2018.
The Geely Group has reached or is close to the level of automotive companies in Europe and America in the design of aluminum alloys, plastics, and lightweight structures. At present, lightweight upgrades and explorations have been carried out in various aspects such as bodywork, chassis, powertrains, and transmission systems. For example, composite material outer covers have begun to adopt materials such as SMC materials and honeycomb composite materials. According to an internal responsible person, “Future Geely will carry out further exploration in the field of carbon fiber composite materialsâ€.
Chery Automobile is also optimising the use of lightweight materials and light weight technology. Three quarters of its body frame materials are made of high-strength steels, and are used in joining processes, laser welding, roll forming, and thermoforming. There has also been a great improvement. It is worth mentioning that the key step for Chery to promote the application of lightweight technology is to establish a weight engineering system and set product weight targets.
Changan Automobile also stated that “we have entered the phase of application of lightweight technology transformation and set a goal: the average weight loss of the main models will reach 50kg by 2020â€.
In addition, the cooperation between domestic auto companies and aluminum-magnesium light metals has become more and more close, and the lighter weight of automobiles has also been further accelerated through the application of aluminum-magnesium light metals. According to electric vehicle resource network, Weilai pure electric SUV - ES8 aluminumization rate of up to 96.4%, the body is made of 7003 aluminum alloy material, chassis, suspension, hub, brake system and battery pack shell are also used aluminum The alloy material has become the world's largest production volume of aluminum alloys in the production of all-aluminum alloys, leading the world automotive aluminization rate.
At the same time, Weilai's pure electric SUV - ES8's instrument panel skeleton and front-end module framework uses magnesium alloy die castings. Undoubtedly, Weilai's pure electric SUV, the ES8, has become an outstanding model of China's own-brand automotive lightweight.
With the dual support of policies and market environment, new energy manufacturing companies need to grasp the opportunities, constantly enhance their own core competitiveness, and strengthen cooperation with upstream material companies in order to promote consumer acceptance of new energy vehicles. The weight of the vehicle is the direction of effort. All in all, lightweight technologies are still evolving, and the road to improvement for companies is still very long.
This Retractable Ceiling Fan has LED module which can switch to different color of light, such as warm light 2500 K, natural light 4500 K and cool light 6000 K. Also this retractable ceiling fan has remote control can allow the owner control the light setting and wind speeds on any where in the house.
Retractable Ceiling Fan With Light,Retractable Ceiling Fan With Light Kit
ZHONGSHAN UFAN ELECTRIC APPLIANCE CO. LTD , https://www.ufanceilingfan.com