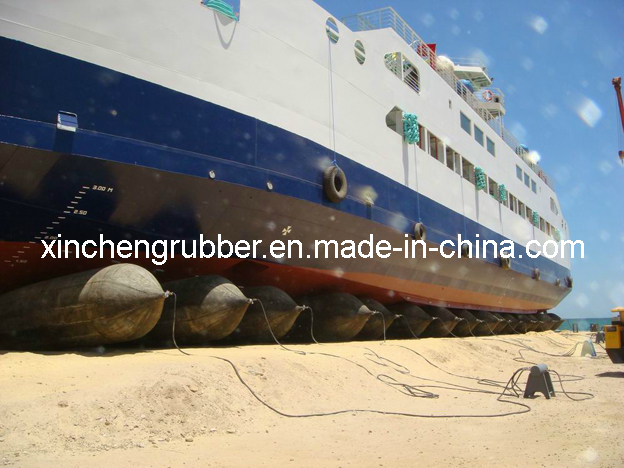
Standard specifications of xincheng Ship Launching Airbags
Diameter (D): From 0.8m to 2.0m.
Effective Length (EL): From 6m to 18m.
Total Length (TL): From 7m to 19.5m
The above specification only is our standard specification arrange. Other specification of ship launching airbags also available upon clients' request.
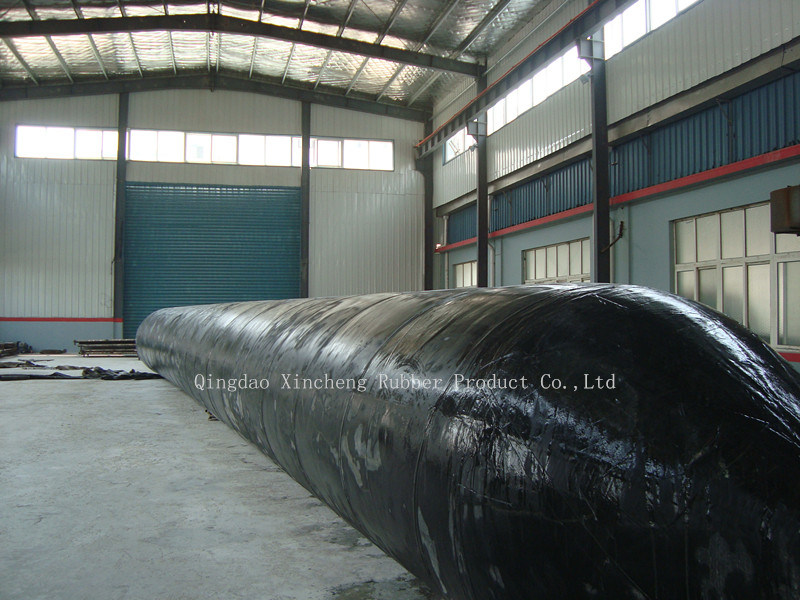
Application:
1. Shipwreck salvage.
2. Floating bridge and dock construction.
3. Rescue and remove of wrecked ship.
4. Can be used as pontoons for supporting docks and other floating structure.
We are a manufacture of airbag, the raw material also manufactured by ourselves, the best quality at the reasonable price. In addition, We promise that the product can be returned due to quality problem within one year; And we provide maintenance technology for free and the required raw material
Cobalt-based alloy powders are commonly used in plasma transfer arc welding (PTAW) due to their excellent high-temperature properties and resistance to wear and corrosion. These alloys are typically composed of cobalt as the base metal, with various alloying elements such as chromium, tungsten, nickel, and carbon added to enhance specific properties.
The use of cobalt-based alloy powders in PTAW offers several advantages, including:
1. High-temperature strength: Cobalt-based alloys exhibit excellent strength and resistance to deformation at elevated temperatures, making them suitable for welding applications that involve high heat.
2. Wear resistance: These alloys have a high hardness and resistance to wear, making them ideal for welding applications where the welded parts are subjected to abrasive or erosive conditions.
3. Corrosion resistance: Cobalt-based alloys offer good resistance to corrosion, making them suitable for welding applications in aggressive environments, such as those involving chemicals or saltwater.
4. Thermal conductivity: Cobalt-based alloys have good thermal conductivity, allowing for efficient heat transfer during welding and reducing the risk of heat-affected zone (HAZ) defects.
5. Compatibility with other materials: Cobalt-based alloys can be easily welded to a wide range of base metals, including stainless steels, nickel alloys, and other cobalt-based alloys, providing versatility in welding applications.
To use cobalt-based alloy powders for PTAW, the powder is typically fed into the plasma arc using a powder feeder. The powder is then melted by the high-temperature plasma arc and deposited onto the workpiece, forming a weld bead. The specific welding parameters, such as arc current, travel speed, and powder feed rate, will depend on the specific alloy and application requirements.
It is important to note that the selection of the cobalt-based alloy powder should be based on the specific welding application and the desired properties of the final weld. Different cobalt-based a
Co Powder,Cobalt 6 Powder,Cobalt 12 Powder,Cobalt 21 Powder
Luoyang Golden Egret Geotools Co., Ltd , https://www.xtcthermalspray.com