The Canadian copper refinery uses pressurized oxygen leaching to dissolve copper and bismuth in the copper anode slime in hot concentrated sulfuric acid. The anode mud composition of the plant is: Cu16%~22%, Se9.6%~15%, Te1.0%~1.6%, Pb8%~12%, Ni0.45%~1.0%, As1.0%~1.5%. , Sb1.2%~2.3%, Bi0.5%~0.9%, Sn1.25%, SiO 2 2.1%, Ba2.2%, H 2 SO 4 14.4%, Ag221kg/t, Au6.2kg/t, Pd600g /t, Pt40g/t. The composition of copper removal anode mud from other copper refineries is: Cu 0.4% to 2.5%, Se 0.2% to 2.8%, Pb 3% to 50%, As 0.05% to 0.2%, Sb 0.1% to 3.2%. Bi is 0.1% to 0.5%, Te is 0.02% to 0.4%, Sn is 0.2% to 0.8%, Ag is 75 to 325 kg/t, and Au is 0.5 to 2.2 kg/t. The anode mud treatment process is shown in Figure 1.

Figure 1 Copper anode slime treatment process in Canadian copper refinery
First, copper, leaching
Pressurized oxygen leaching allows most of the copper and bismuth to leach, while silver selenium remains in the slag. The response is:
Cu+H 2 SO 4 +1/2O 2 =CuSO 4 +H 2 O
Cu 2 Se+2H 2 SO 4 +O 2 =2CuSO 4 +Se+2H 2 O
2CuAgSe+2H 2 SO 4 +O 2 →2CuSO 4 +Ag 2 Se+Se+2H 2 O
2Cu 2 Te+4H 2 SO 4 +5O 2 +2H 2 O=4CuSO 4 +2H 6 TeO 6
The anode mud was filtered by centrifugation, and the filter cake was pulverized with water and 93% sulfuric acid in a stirred tank, and then pumped into an autoclave (material 904L stainless steel). The autoclave was equipped with a center baffle and a 6 kW motor driven 6-blade turbine agitator. The material was heated to 125 ° C, the oxygen pressure was 275 kPa, and the total leaching time per batch was about 3 h. The leaching mud is sent to a frame filter press for filtration and washed with warm water. The leaching slag rate is 70%, which contains 0.3% to 0.5% copper and 0.5% to 0.9% lanthanum.
The pressure infusion tellurium with copper scrap metal is precipitated as Cu 2 Te, through the air leaching with NaOH (formation of soluble Na 2 Te), sulfuric acid adjusted to pH 5.7, precipitated TeO 2; redissolved with NaOH solution to form a碲 electrolyte. The response is:
H 6 Te 6 +5Cu+3H 2 SO 4 =Cu 2 Te↓+3CuSO 4 +6H 2 O
2Cu 2 Te+4NaOH+3O 2 =2Na 2 TeO 3 +2Cu 2 O+2H 2 O
Na 2 TeO 3 +H 2 SO 4 =TeO 2 ↓+Na 2 SO 4 +H 2 O
electrolysis
Na 2 TeO 3 +H 2 O→Te+2NaOH+O 2
Second, drying, granulating, roasting
In the copper mud after decoppering and crucible, selenium is mainly present as an element or Ag 2 Se. Selenium melts at 217 ° C, burns at 200-220 ° C, and a large amount of SeO 2 is produced at 260-300 ° C. Ag 2 Se starts to oxidize to strontium selenite at 410-420 ° C, and rapidly forms at 500 ° C, Ag at about 530 ° C. 2 SeO 3 melts and decomposes slowly below 700 ° C, so that the charge is sintered, hindering the oxidation and volatilization of selenium. The following steps can be used to improve: (1) adding 5% to 10% bentonite mixed with anode mud to adsorb Ag 2 SeO 3 melt; (2) granulating and soda roasting, so that selenium is dissolved in water Soluble sodium selenate Na 2 SeO 3 form solid; (3) granulation and calcination in a static bed, forced circulation of high temperature air.
For example, the pressurized oxygen leaching residue is dried in a rotary kiln to 8% of sweat, and then mixed with 5% to 10% bentonite, and placed on a Φ370 mm inclined disc granulator for granulation, the ball diameter is 10 mm, and the granulation capacity is 675 kg/ h; green pellets were calcined in a sintering machine at 815 ° C for 1 to 2 h, and the air was bubbled to 30 m 3 /min. SeO2 containing soot is washed with water to form Se100g/L H 2 SeO 3 solution, and then passed into SO 2 to reduce it to elemental selenium; wet granules can also be calcined in three movable bed tower burners. a thickness of 20 ~ 30mm, width 7.5m bed firing, 12.2m length, the bed, beneath the coal gas burner heating, residence time of about 60min. The temperature is controlled at 800 to 820 ° C to rapidly oxidize Ag 2 Se.
Third, the reverberatory furnace smelting
The above-mentioned pretreated material is smelted in a suspended reverberatory furnace (internal size: 2.13 m × 6.17 m, solution tank depth 0.38 m) made of high-quality refractory material to obtain a gold-silver alloy. The general smelting operation cycle is 50-60h, including charging, melting, smelting, slag, oxygen and air blowing, oxygen blowing and soda slag and casting anode. 800 anodes per furnace (7.775kg each).
Fourth, gold and silver alloy smelting slag flotation
The slag extracted from the smelting furnace contains a large amount of matte and metal, usually returned to copper smelting, which can improve the degree of impurity removal, but increases the loss and balance of gold and silver. The Canadian refinery installed a small flotation plant that has recovered 6000 kg of silver and 90 kg of gold from the backlog of slag and produces about 80 to 90 tons of slag flotation tailings per day.
Five, top blowing converter
The Canadian copper refinery changed the traditional gold-silver alloy smelting reverberatory furnace to a top-blown converter. The current furnace has a working capacity of 1300L, which can reduce the precious metal backlog (about 22.6t silver, 0.6t gold) and save costs. However, all materials must be dried and granulated as much as possible; however, the flue gas system is heavily loaded and will oxidize more silver, which is not easily recovered in the slag flotation circuit. In addition, there is more lead entering the flue gas, increasing the load on the lead cycle.
Sixth, the gold
The gold-silver alloy anode is electrolyzed in a vertical electrolytic cell. The cells were arranged in 12 groups, each group was connected in series with 5 slots, and the power was supplied in groups (1000 A, 22 V). The silver powder deposited on the titanium cathode was continuously peeled off with a mechanical scraper, collected in a basket suspended under the cathode, lifted up in 24 hours, discharged, washed, dried, and then smelted in an induction furnace to cast a silver bar of 31.1 kg. It is Ag99.99%, Se0.0001%, Au0.0011%, Cu0.0041%, Pb0.0003%, Pd0.0003%. Silver anode mud (gold or black gold powder) is retained in the polyester bag of silver anode mud.
Seven, gold refining
The gold slag is discharged once every three days, and the composition is: Au 39% to 62%, Ag 24% to 50%, Pb 3.5% to 5.6%, Cu 2% to 5%, and Pd 0.2% to 0.6%. Was washed to remove soluble nitrates, then concentrated sulfuric acid in a digester tank heated cast iron, silver down to acceptable levels. The gold powder is filtered and washed until the filtrate no longer contains silver, and is smelted in an induction furnace, and then the anode mud is cast for gold electrolysis.
Platinum , palladium and gold are dissolved together from the anode and accumulate in the electrolyte. When Pd exceeds 70-80 g/L, gold will be deposited on the cathode and contaminated, so purification must be carried out frequently.
Eight, platinum, palladium recycling
The gold electrolysis waste liquid is diluted with 2 times of water and neutralized with an alkaline solution to pH=5-6. At a temperature of 90-100 ° C, oxalic acid is added to the solution to precipitate gold (2AuCl 3 +3H 2 C 2 O 4 2H 2 O→2Au↓+6HCl+6CO 2 +2H 2 O). The solution was heated with steam and alternated with the gold precipitation operation until the reaction was stopped and decanted; the decanted liquid was neutralized to pH = 6, and the residual gold was again precipitated.
The gold leaching filtrate is heated to about 80 ° C, sodium formate is added and stirred. Platinum and palladium are easy to precipitate, washed, filtered and dried to obtain a platinum-palladium concentrate. The general composition is: Pd 20% to 85%, Pt 5% to 12%, Au0. 02% to 0.2%, Ag 0.5% to 0.8%; other platinum group metals are few, about (10 to 50) × 10 -4 %.
EVA Deck Pad for kiteboard deck pad and SUP deck pad comes in two ways normally. One is full sheet for DIY, the other one is die cutting based on customized design.
The full sheet deck pad can be in 230cm x 90cm or 90cm x 90cm size. Customers can cut the deck pad based on their board size, then simply peel and stick since the EVA deck grip we offered it with 3M adhesive. Besides, it can be also used in any other application for traction like boat flooring, yacht flooring and etc.
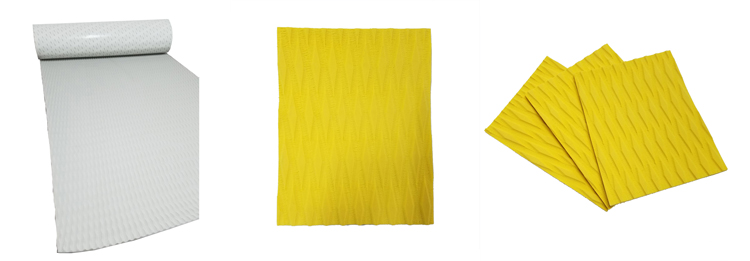
Eva Deck Pad,Surfboard Tail Pad,Kiteboard Deck Pad,Deck Grip Mat,Sup Board Deck Grip,Traction Deck Pad
Huizhou City Melors Plastic Products Co., Limited , https://www.melorsmarine.com