Complex phosphate mineral composition of different types of ore, since the differences in mineralization conditions, and the content of mineral species, disseminated grain size, structure and other structures, and the degree of difficulty selected from other processes are quite different. Phosphate ore is classified into siliceous phosphate rock, calcareous phosphate rock and siliceous calcium phosphate rock according to the chemical composition of minerals. For different ore types, the sorting process is different. At present, the process of sorting phosphate rock applied at home and abroad is relatively perfect, but each has its own advantages and disadvantages. The following is a brief introduction to the more common processes.
First, positive flotation process
The process is generally used for sorting low grade phosphate rock, silica and silicon processing including calcium phosphate, calcium and magnesium phosphate quality. The process must have a combination of inhibitory inhibitors to achieve satisfactory results, mainly for the minerals in which the phosphorus minerals and gangue minerals are finely embedded. In recent years, L series and S series high-efficiency inhibitors have been successfully developed, which can obtain better flotation effect on sedimentary metamorphic phosphate rock, but only for ore with low Mg0 content, and direct filtration of products is difficult. It limits the application and promotion of this process in phosphate rock production in China.
Second, the reverse flotation process
The process is mainly applied to the separation of phosphate rock and dolomite. The fatty acid is often used as a collector in the weakly acidic medium. The product in the dolomite floatation tank is a phosphate concentrate. The discharge rate of dolomite is generally up to -80. %. The discharge rate of dolomite and the loss rate of P 2 O 5 are generally (6 to 10):1. However, it cannot separate siliceous gangue. At the same time, there are shortcomings such as fine particle size, difficulty in transportation and handling of foam products, and there are still problems in finding collectors with appropriate collection performance, good selectivity and excellent inhibitors. Wu Yanni and others used the reverse flotation process of three-stage dosing and three-sweeping in the rough selection, and obtained a satisfactory selection index. When the ore P 2 O 5 grade is 27.07%, the MgO content is 4.22%, and the grinding fineness is -0.071 mm (-200 mesh) 66.4%, P 2 O 5 grade can be obtained by using phosphoric acid as a reverse flotation inhibitor. The high-quality phosphate concentrate with 32.91% and Mg0 of 0.92% has a P2O5 recovery rate of 92.88% and a MgO removal rate of 83.33%.
Third, the positive and negative flotation combined process
In order to overcome the shortcomings of the positive flotation and reverse flotation processes, the siliceous calcium phosphate ore can be treated by a combination of positive and negative flotation processes. The process is to first float the carbonate in a weakly acidic medium, and then float the silicate in an alkaline medium (regrind or not), since the hardness of the carbonate is lower than the hardness of the phosphorus mineral, In the process of mining, it is easy to break and is preferentially dissociated. The purpose of the second stage of the reverse flotation process is to improve the subsequent performance of the phosphate concentrate (ie, reduce the content of MgO), rather than to improve the concentrate grade. Another advantage of the positive and negative flotation process compared to other flotation processes is that its final concentrate is in the tank, has a coarser particle size, and is easier to dewater than a foam product.
Deng Wei and so on for the refractory Qingping low-grade silicon-calcium phosphate rock, using the full sulfuric acid positive and negative flotation process, in the original ore P 2 O 5 22.22%, MgO 2.91%, and grinding to -200 mesh 93% Under the condition of continuous test, the continuous test run for 72 h, the process technical index of concentrate grade P 2 O 5 30.37%, MgO 0.53%, concentrate yield 60.71%, recovery rate 82.99% can be obtained, the process floats at room temperature, and There are few types of flotation reagents and the cost of medicines is low.
Four, double reverse flotation process
Double reverse flotation is the first reverse flotation of dolomite, and then reverse flotation of silicate, the product in the tank is the final phosphate concentrate. The process can be carried out under normal temperature and coarser particle size conditions. Compared with the positive and negative flotation combined process, the conditions of flotation silicate gangue are different. The positive and negative floating combined process is to make the surface of the silicate positively charged under alkaline conditions and to separate from the target mineral by an anion collector, and the double reverse float overcomes the shortcomings of the difference between the acidity and alkalinity of the positive and negative floating combined process. . Zeng Xiaobo used the de-magnesium collector SR agent, a coarse two-sweeping agent and a de-siliconization agent GE-609, a coarse-sweep double-reverse floatation process, and obtained a satisfactory index: P 2 O 5 27.27% of the original ore mill When the ratio is -0.074mm to 75%, the comprehensive concentrate yield is 72.69%, the P 2 O 5 grade is 32.87%, the recovery rate is 86.93%, and the harmful impurities are magnesium and aluminum. iron are significantly reduced: ore containing MgO2.25%, Fe 2 O 3 1.87 %, A1 2 O 3 3.11%, the concentrate containing MgO0.93%, Fe 2 O 3 1.17 %, A1 2 O 3 1.45%.
On the other quiet ore containing P 2 O 5 24.69%, MgO 3 .173%, SiO 2 14.57% ore in grinding fineness of 85% -200 mesh conditions, using double reverse flotation, P 2 can be obtained O 5 32.48%, MgO 0.42% phosphorus concentrate, concentrate yield 65.28%, P 2 O 5 recovery rate 85.88%, magnesium removal rate 91.36% process indicators, the process drug system is simple, the required types of chemicals are small, The sorting efficiency is high, the process index is excellent, and the final concentrate is a product in the tank, which is easy to dehydrate.
In addition to the above several flotation processes, there are also a phosphorus selective joint process of the phosphate rock, a heavy medium sorting process, a photoelectric selection-flotation, a roasting-digestion-flotation process, and the like.
Rotary activation furnace is an internally heated fluidized bed continuous production activation furnace. The activator is water vapor and flue gas. This method is also used in the production of wood charcoal.
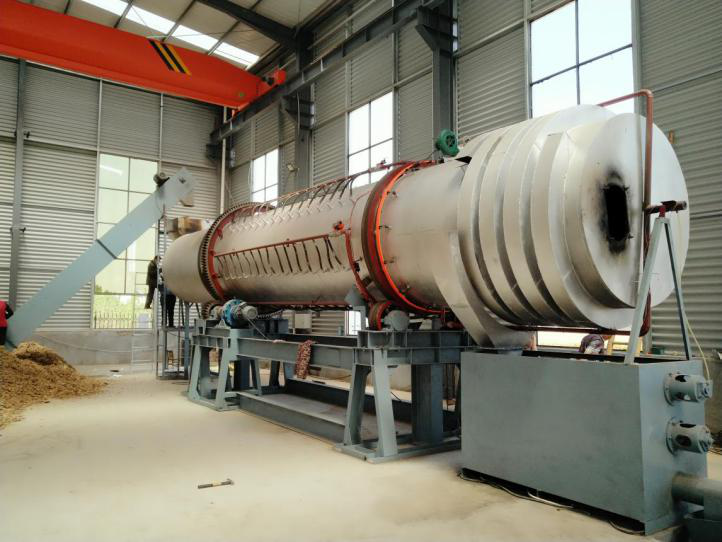
If you have any questions, please contact with us directly. Welcome you can visit our Factory.For inqury,Please send mail directly to us.
Rotary Activated Stove,Activated Carbon Activation Furnace,Activated Carbon Production Machine,Activated Carbon Processing Equipment
Shandong Hengyi kaifeng Machinery Co.,Ltd , https://www.xhykf.com