A few days ago, Volvo announced that it will conduct an independent KERS system R&D test with the aim of developing the KERS system into mass production vehicles. Volvo said that KERS can be seen as a lightweight and relatively inexpensive hybrid system that can make a 4-cylinder car with the same power as a 6-cylinder car, while reducing emissions by about 20%.
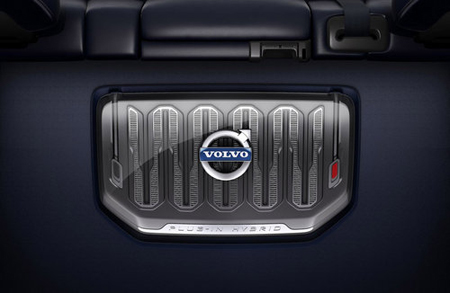
The KERS (dynamic energy recovery system) technology has been used in the F1 race for some time. I believe many people are familiar with it and Porsche has successfully installed it on the 911 GT3 R Hybrid.
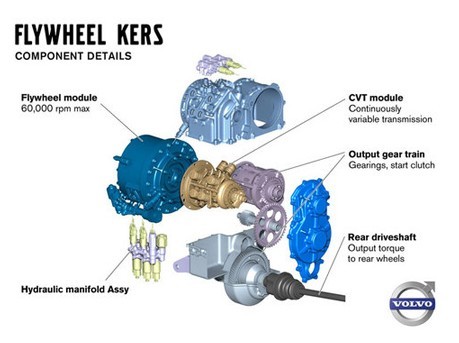
The Volvo KERS system designed by Volvo is installed on the rear axle of the vehicle and is responsible for driving the rear wheels. When the driver brakes, the energy generated by the brake will cause the flywheel to move at a rate of 6,000 revolutions per minute, and when the vehicle is restarted, the system converts the kinetic energy of the flywheel to the rear axle to help drive the vehicle. In addition, once the KERS system is started, the gasoline engine responsible for driving the front wheels will stop working because the energy stored in the KERS system is sufficient for the car to start accelerating again, and the gasoline engine will not be restarted until its energy is consumed.
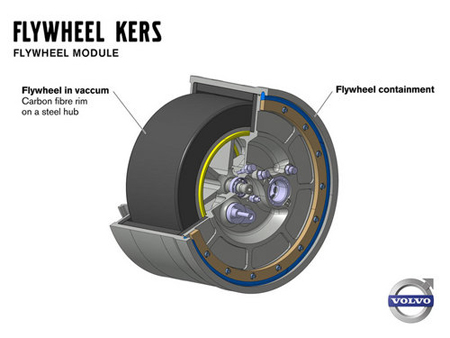
The flywheel KERS system can provide an additional 58 kilowatts of power (80 hp) when the energy is fully loaded. Volvo expects that the gasoline engine of the vehicle will be turned off for half the time under normal urban road conditions. One of the characteristics of Volvo's flywheel KERS system is its carbon fiber structure. Its flywheel has a net weight of only 5 kg and a diameter of about 20 cm. Moreover, the environment in which the flywheel is located is hermetically sealed, thus reducing the frictional resistance during movement.
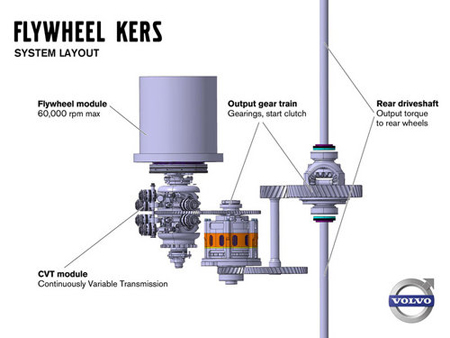
Compared to the traditional hybrid system, the flywheel KERS system does not have expensive battery packs and electronic control modules and the cost is relatively low. If the experiment is successful, Volvo production models equipped with a KERS system will be seen in the next few years.
GYQ drilling rig is an upgraded and improved product of GXYdrilling rig. It mainly adds the winch detachment
function structure, thereby extending the service life of the hoist. This drilling rig is a vertical transmission rotary drilling
rig with mechanical transmission and hydraulic feed. It can be applied to engineering geological survey, general survey of
solid deposits, grouting of dams and ventilation and drainage of tunnels. Depending on the drilling formation, cemented
carbide, steel grit, and auger types can be used for drilling.
Main Feature:
The structure of this rig has the following features:
1. A more reasonable speed range is selected. There are eight speed levels, centralized speed change, self-locking with
each other, large low-speed torque, and a wide range of use.
2. The drilling rig has two speeds of reversing speed, which is convenient for handling faults safely.
3. The self-centering hydraulic chuck is adopted, which is convenient for clamping and loosening the drill pipe. And has
a hydraulic feed mechanism, strong pressure and lifting capacity.
4. Equipped with sufficient instruments, it is helpful to grasp the situation in the hole, fewer operating handles, more
reasonable layout, flexible and reliable operation.
5. The two-plate normally closed friction clutch is adopted, which is flexible to open and close, and easy to adjust and use.
6. The rig is light in weight, compact in structure, easy to disassemble, and suitable for drilling work in hills or mountains.
7. The hoist has a detachment function. Increased the service life of the hoist.
Gyq Drilling Rig,Gyq Survey Machine,Gyq Survey Rig,Spindle Core Drilling Rigs
JIANGSU XI TEC ENVIRONMENTAL&DRILLING EQUIPMENT COMPANY CO.LTD , https://www.xitecdrillingwx.com