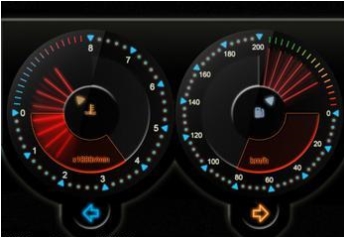
1, before the analysis of field instrument failures, it is necessary to thoroughly understand the relevant instrument system production process, production process conditions and conditions, understanding of the instrument system design, design intent, instrument system structure, characteristics, performance and parameter requirements.
2. Before analyzing and inspecting the fault of the field instrument system, the operator should be informed of the changes in the production load and the parameters of the raw materials, view the recording curve of the fault meter, and conduct a comprehensive analysis to determine the cause of the instrument fault.
3. If the instrument records a dead line (a line with no change is called a dead line), or the record curve originally fluctuates, it suddenly becomes a straight line; the fault is likely to be in the instrument system. Because the current recording instruments are mostly DCS computer systems, the sensitivity is very high, and the change of parameters can be very sensitive to the reaction. At this point can artificially change the process parameters to see the curve changes. If it does not change, the basic conclusion is that the instrument system has a problem; if there is a normal change, it is basically determined that the instrument system has no major problems.
4. When the process parameters are changed, it is found that the recorded curve has abruptly changed or jumped to the maximum or the minimum. At this time, the fault is often in the instrument system.
5, before the fault appeared instrument record curve has been normal, after the occurrence of fluctuations in the recording curve becomes irregular or difficult to control the system, and even manual operation can not control, this time the fault may be caused by the process operating system.
6. When it is found that the DCS display instrument is abnormal, you can go to the site and check the indication value of the same intuitive instrument. If they are very different, it is likely that the instrument system has failed.
In short, when analyzing the causes of field instrument failures, special attention must be paid to the changes in the characteristics of the measured control object and the control valve, which may be the cause of the failure of the field instrument system. Therefore, we must comprehensively consider and carefully analyze the field instrument system and process operating system to check the reason.
French Skin Care Raw Material PDRN,Korean Skin Care Raw Material PDRN,European Skin Care Raw Material PDRN
Ruijiming (Shandong) Biotechnology Co., Ltd , https://www.mgpdrn.com