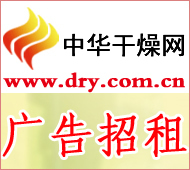
As raw material titanium concentrate prices continue to rise, and there is no sign of abating, some international titanium dioxide producers have raised the wave of price increases in Asia in the second quarter in order to eliminate the impact of rising costs.
DuPont and Cristal Global have announced that they will raise the price of products in Asia from April 1st to 200 US dollars (tons, the same, CFR, Asia), Kronos and Tenor. Afterwards, it also announced a price increase of $250 for the second quarter. Huntsman and Japan's Ishihara Sangyo Co., Ltd. rose even more, raising prices by $300 and $400, respectively. According to the ICIS data, as of March 30, the latest price of Asian titanium dioxide is 4000 to 4200 US dollars (CFR, Asia). Since the beginning of this year, the price of titanium dioxide in Asia has been at this level.
Some producers stated that it is necessary to increase the price to offset the skyrocketing price of raw titanium ore. Since the second half of 2011, some ilmenite ore prices have increased by 70% to 75%. A Japanese manufacturer even claimed that a price increase of $200 is not enough to offset the raw material inflation factor. Some market participants predict that due to the global economic slowdown, this year's titanium dioxide market will not reproduce the strong growth momentum as in 2011, but as the price of raw material titanium concentrate continues to rise, the price of titanium dioxide will remain firm. According to the ICIS data, the price of titanium dioxide in Asia rose by 1,200 U.S. dollars in 2011, which is about 40% higher than the price of 2,800 to 3,000 U.S. dollars (CFR, Asia) at the beginning of 2011.
Asbestos was added as an common ingredient to Brake Pads post-WWI, as car speeds began to increase, because research showed that its properties allowed it to absorb the heat (which can reach 500 °F) while still providing the friction necessary to stop a vehicle. However, as the serious health-related hazards of asbestos eventually started to become apparent, other materials had to be found. Asbestos brake pads have largely been replaced by non-asbestos organic (NAO) materials in first world countries. Today, brake pad materials are classified into one of four principal categories, as follows:
Non-metallic materials - these are made from a combination of various synthetic substances bonded into a composite, principally in the form of cellulose, aramid, PAN, and sintered glass. They are gentle on rotors, but produce a fair amount of dust, thus having a short service life.
Semi-metallic materials - synthetics mixed with varying proportions of flaked metals. These are harder than non-metallic pads, more fade-resistant and longer lasting, but at the cost of increased wear to the rotor/drum which then must be replaced sooner. They also require more actuating force than non-metallic pads in order to generate braking torque.
Fully metallic materials - these pads are used only in racing vehicles, and are composed of sintered steel without any synthetic additives. They are very long-lasting, but require more force to slow a vehicle while wearing off the rotors faster. They also tend to be very loud.
Ceramic materials - Composed of clay and porcelain bonded to copper flakes and filaments, these are a good compromise between the durability of the metal pads, grip and fade resistance of the synthetic variety. Their principal drawback, however, is that unlike the previous three types, despite the presence of the copper (which has a high thermal conductivity), ceramic pads generally do not dissipate heat well, which can eventually cause the pads or other components of the braking system to warp.However, because the ceramic materials causes the braking sound to be elevated beyond that of human hearing, they are exceptionally quiet.
Truck Brake Pads,Z36 Brake Pads,New Brake Pads,Best Brake Pads For Trucks
LIXIN INDUSTRIAL & TRADE CO.,Limited , https://www.jmsparkplug.com